How Defoamers Are Used to Prevent Foam in Food and Beverage Production
How Defoamers Are Used to Prevent Foam in Food and Beverage Production
Blog Article
Picking the Right Defoamer for Your Details Application Requirements
Selecting the appropriate defoamer for certain application requirements is a nuanced procedure that demands careful factor to consider of numerous factors, such as the foam operating, kind, and tool conditions. Recognizing the subtleties of defoamer performance-- including rate and perseverance-- while also accounting for ecological and regulatory elements is vital.
Understanding Foam Development
Foam development takes place when gas is entraped within a fluid, creating a steady framework of bubbles. This phenomenon can dramatically affect numerous commercial processes, specifically in markets such as food manufacturing, pharmaceuticals, and wastewater therapy. The existence of foam can prevent blending, lower product top quality, and even bring about operational inefficiencies.
Foam normally forms because of a combination of factors, consisting of surface-active agents, frustration, and the qualities of the liquid phase. Surfactants reduced the surface area stress of the fluid, promoting the formation of bubbles that can coalesce and stabilize. Frustration, whether from mechanical mixing or gas intro, enhances bubble development, bring about increased foam volume.
Understanding the mechanics of foam development is vital for sectors intending to maximize their procedures. By determining the certain conditions that advertise foam generation, organizations can execute techniques to mitigate its results.
Kinds of Defoamers Available
Different kinds of defoamers are readily available to resolve the difficulties positioned by foam in industrial applications. defoamers. Extensively identified, defoamers come under three groups: silicone-based, non-silicone-based, and natural defoamers
Silicone-based defoamers are renowned for their effectiveness and security across a wide variety of temperatures and pH degrees. They are generally made use of in applications where strong foam suppression is needed, such as in paints, coatings, and adhesives. Their reduced surface area tension enables rapid foam collapse.
Non-silicone-based defoamers, frequently made from natural substances, use a choice for applications sensitive to silicone residues. These defoamers can be further separated right into polyether and ester kinds, each tailored to satisfy details formula demands. Non-silicone defoamers are frequently used in food processing and individual treatment items due to their compatibility with different formulations.
Natural defoamers, stemmed from plant or animal sources, are getting grip as a result of their green account. These items are specifically appealing in applications where governing conformity and sustainability are vital, such as in agrochemicals and biotechnology.
Picking the best sort of defoamer is crucial for maximizing efficiency and guaranteeing compatibility with certain applications.
Secret Application Factors To Consider
When picking a defoamer, it is important to take into consideration the specific application requirements to make certain optimum efficiency. defoamers. Various sectors have distinctive requirements, such as food processing, drugs, or wastewater therapy, and each application may require special defoaming properties
Secret variables to assess consist of the medium in which the defoamer will be used, whether it is water-based, oil-based, or a mix thereof. The temperature and pH degrees of the application can likewise greatly affect the efficiency of a defoamer. Additionally, compatibility with other chemicals existing in the system is vital to stop negative reactions that could endanger performance.
Another important consideration is the frothing behavior of the particular system. Comprehending whether the foam develops rapidly or slowly can direct the option of a defoamer that targets the source successfully. Furthermore, the wanted speed of defoaming can affect the option, as some applications require quick activity while others might endure slower defoaming procedures.
Finally, ecological and regulative considerations must not be neglected, specifically in industries with strict conformity demands. Picking a defoamer that lines up with these factors makes certain both performance and safety in the application.
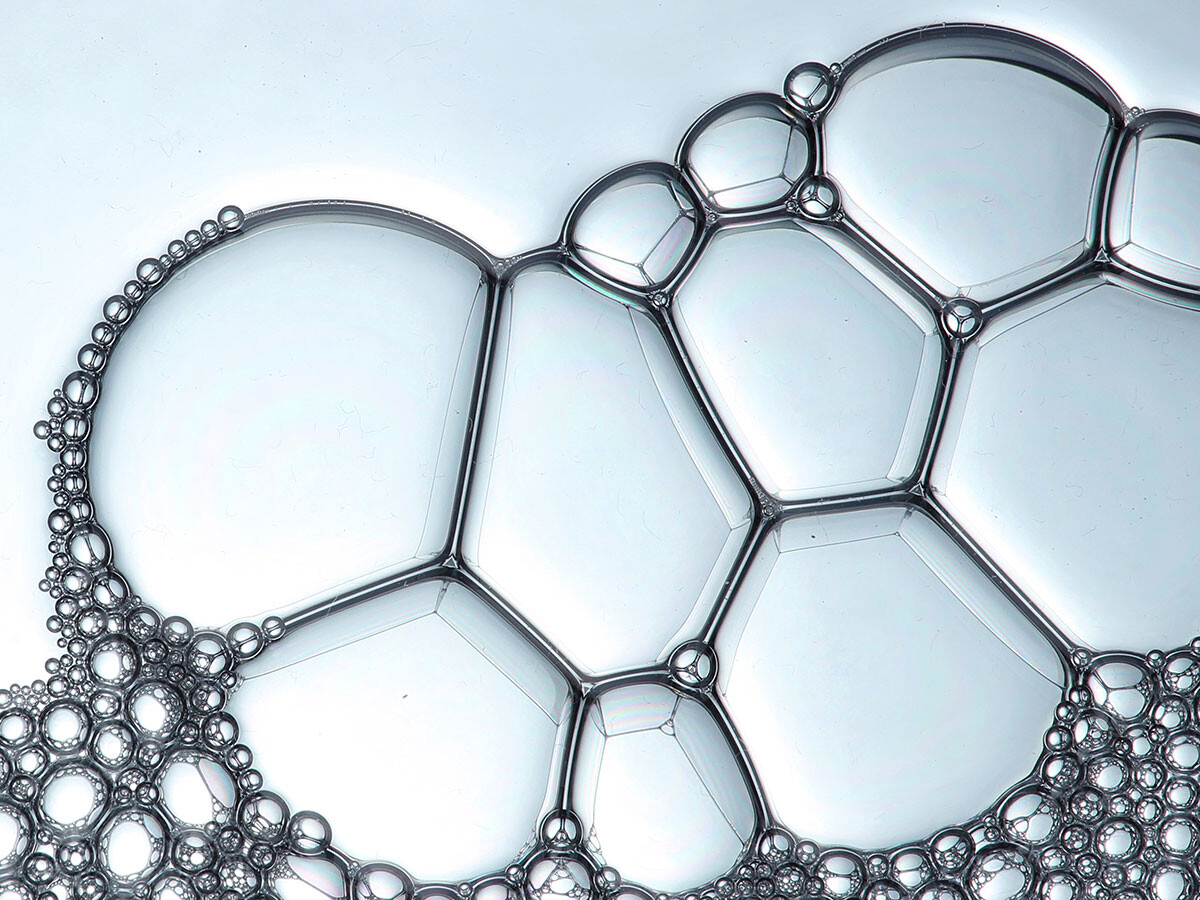
Efficiency Testing Techniques
Assessing the performance of a defoamer needs a systematic method to testing that precisely determines its effectiveness in specific applications. Different efficiency screening approaches can be used to determine the optimum defoamer for a given formulation.
One typical approach is the bubble test, which evaluates the defoamer's ability to decrease foam quantity gradually. This test entails producing a steady foam and then including the defoamer to observe the price of foam collapse. One more method is the dynamic foam test, where foam is produced under regulated conditions to mimic real-world application circumstances. This strategy supplies understandings right into exactly how the defoamer does under varying shear conditions.
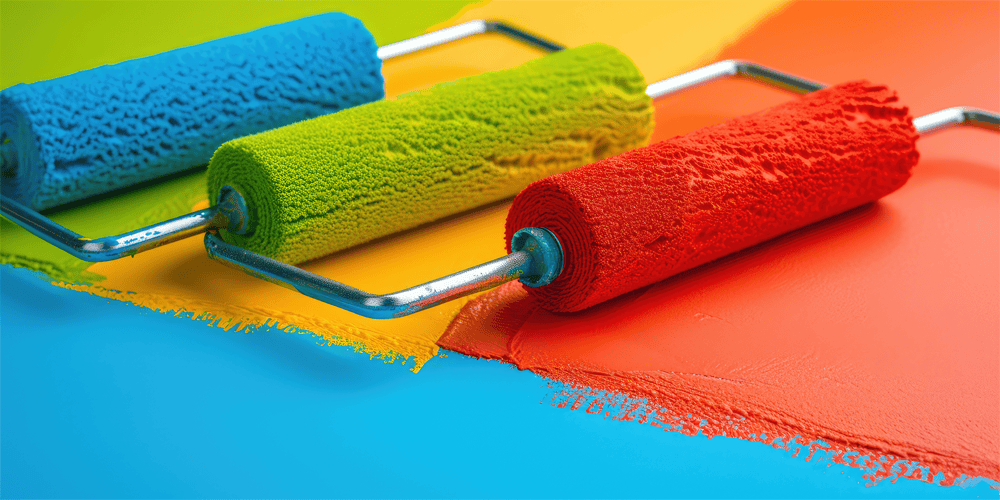
Ultimately, picking the suitable performance screening look at this web-site method depends on the certain application and the type of foam being attended to. Each method supplies important information that can direct formulation adjustments and improve the effectiveness of the defoamer in practical applications.
Ideal Practices for Option
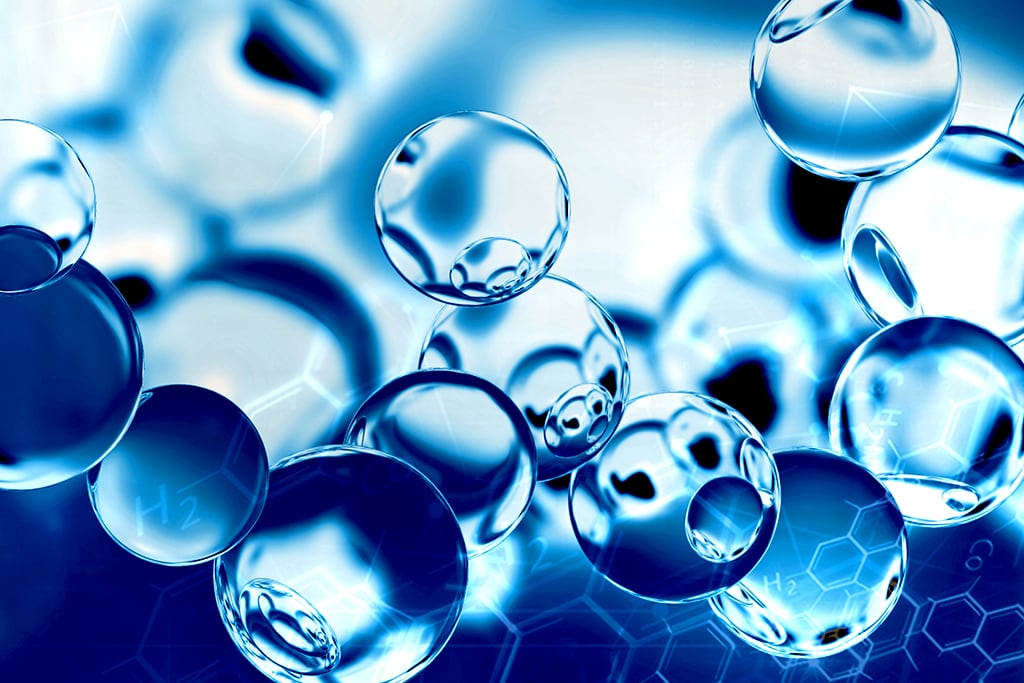

Next, take into consideration the defoamer's performance in regards to speed of action and determination. A quick-acting defoamer may be required for procedures where quick foam reductions is critical, while an extra consistent formulation could be required for long term foam control. In addition, assess the environmental impact of the defoamer, including its biodegradability and any kind of regulative compliance requirements.
Conduct tests with selected defoamers to establish their effectiveness in real-world conditions. By adhering to these finest practices, you can improve foam control effectiveness and guarantee the durability of your processes.
Final Thought
In summary, selecting the ideal defoamer demands a comprehensive evaluation of various variables, including foam kind, medium, operating conditions, and ecological considerations. Recognizing the special attributes of foam formation and the readily available defoamer options is important.
Picking the proper defoamer for details application demands is a nuanced process that requires careful factor to consider of multiple variables, such as the foam operating, type, and tool you can look here conditions.Choosing the ideal defoamer is important for achieving ideal efficiency in foam control applications. A quick-acting defoamer might be required for procedures where quick foam suppression is important, while a more relentless solution might be required for prolonged foam control.In recap, choosing the proper defoamer necessitates an extensive assessment of numerous variables, consisting of foam type, tool, operating problems, and environmental factors to consider. Comprehending the one-of-a-kind characteristics of foam formation and the Homepage readily available defoamer choices is crucial.
Report this page